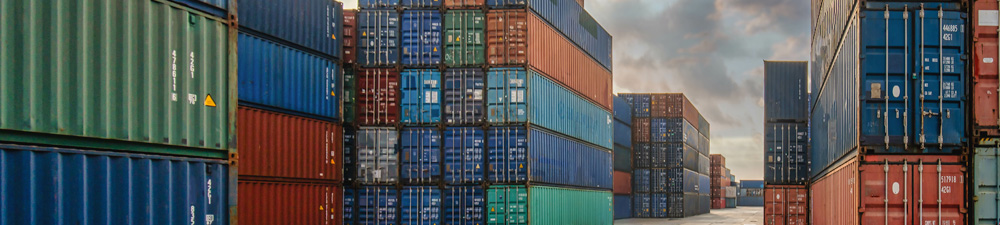
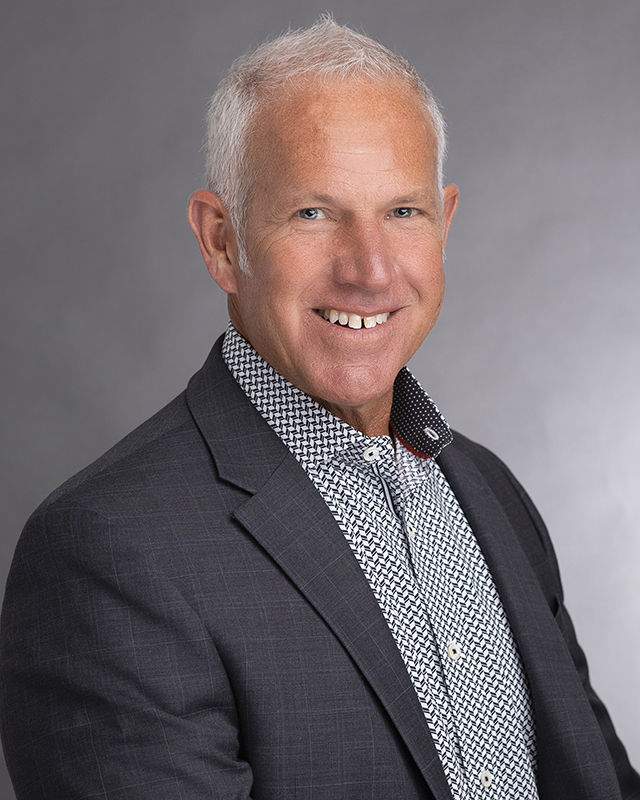
Ron Berg
COO, SVP, Supply Chain
The Year of the Tiger has arrived. Yet, as you know, on the supply chain side this Lunar New Year still very much favors the tortoise. For distribution companies across industries, slow and steady is today’s only option. But that doesn’t mean all we can do is exercise patience.
To level set, let’s acknowledge that the prolonged public holiday in China is indeed an annual supply chain disruptor. It’s a forecast hiccup built into inventory planning year over year. It’s intricate, but manageable – unless, of course, an unprecedented global pandemic triggers an unparalleled global supply chain slowdown, for two years and counting. It’s only natural that China, the world leader in manufacturing, remains at the center of this ongoing challenge.
Shipping container shortage
When we think back, for many Americans the pandemic arrived in early 2020. The sports-minded tend to pinpoint March 12, which is when the National Basketball Association (NBA) abruptly suspended its season. But quarantines, furloughs, and shutdowns were also taking hold well beyond our shores. The inevitable global ripple effect unfolded in sequences and traveled divergent paths.
For example, China valiantly responded to the initial need for personal protective equipment (PPE) by revamping its factories and sending PPE-filled cargo vessels across the globe. However, empty shipping containers began piling up in far-flung locales just as demand was shifting back to consumer goods. Of course, it soon became a tsunami of a shift to consumer product sales. Pandemic relief packages gave most consumers excess spending capital. With limited brick and mortar options and virtually no real leisure and travel afoot, ecommerce exploded.
For this and other interrelated reasons, the shipping container shortage persists – and its bottom-line impact is significant. Last fall, our company needed roughly 15 containers to fulfill just a small segment of our inventory orders. Due to the shortage, we received only two containers. With hotel properties eager to restock, that’s lost opportunity. Even more deflating, the cost on these containers has continued to multiply, now up to five and six times per container compared to pre-pandemic costs.
Port congestion, plus infections
We all know our vital West Coast ports remain heavily congested, which means many ships with full containers still idle offshore, sometimes for weeks, awaiting their turn to dock and unload. The dramatic fluctuation in trucking employment is another factor that continues to antagonize the physical flow of commerce.
While we collectively celebrate Chinese New Year, it is a delicate time for a supply chain that has already had to withstand so much. Given its standing as the world’s second largest economy and a logistical force in global trade, China’s every move invariably influences the level of supply pain.
Just last week China instituted lockdowns, part of its zero-Covid strategy, after infections were reported in key port cities. The Winter Olympic Games in Beijing are now underway, adding another potential disruption in the link. Some analysts expect to see a limited number of shipments coming out of China over the next few months.
Action steps, long-term optimism
For now, slow and steady is a mantra we embrace. But we’re also acting on intelligence every day. To help our customers stay guest ready, we’re analyzing real-time data and placing orders based on realistic end-to-end delivery estimates. We’re finding ways to prod the process at every turn. That means working with every major shipping company and exploring every shipping route. Our distribution teams execute on a series of steps, including:
- Tracking arriving shipments daily
- Continue to model cost impacts
- Work with suppliers to arrange shipments
- Network with related businesses to assess conditions
- Creatively finding alternate shipping lanes (logistics) to ship ASAP at the best price
At CHS, we are making real progress in our inventory gains and our lead times. But we firmly understand progress is, in most cases, marked with an asterisk. For example, right now we have 80 containers of product on vessels that are on the water. That is movement, with an asterisk.
As mentioned, port congestion and land-based logistics have kept ships from coming ashore. The ports of Los Angeles and Long Beach handle 40% of U.S. imports. On February 1, 2021, 40 container ships were waiting offshore. This November 1, there were 101.
Whether it’s idling ships, limited containers, the Omicron wave, or Chinese New Year, we recognize there is no perfect recipe to combat the supply chain slog, and no silver bullet to quickly resolve it. Even as we see progress, the fits and frustrations will continue. As one shipping trends publication put it, “A growing consensus now suggests that the current supply chain chaos will last at least throughout 2022.”
For our part, we will pay close attention to every aspect of supply, with every intention to get essential products to properties as soon – and as cost-effectively – as possible. We will also keep you informed as we navigate the road ahead, together.